LWRはドイツの航空宇宙研究所が開発した新世代産業用ロボット(関節トルク制御方式)であり、SME(中小量生産)向けに開発されたものである。基本的には米国Robotics Rsearch社のロボット(K-*i型)と同じ設計コンセプトであり、その改良版とも言える位置づけのものだ。しかし、その動きをWebビデオで見る限り、LWRのほうが実用的な性能(速さ、加減速度、騒音、大きさ、扱える質量など)は相当に高まっていると思われる。(参考:LWRのビデオ、およびRobotics ReserachのK1207i ロボットのビデオ)
日本では関節トルク制御方式のロボットで商品化されているものはまだ無い。
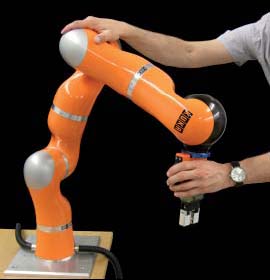
写真:KUKA社製のLight-weight robot。SME robot のDownload ページのSafety in Human-Robot Interactionから引用。ロボットのどの部分を押しても動かすことができる。KUKA社はこのロボットをまだ社内で評価中で、市販はしていない。
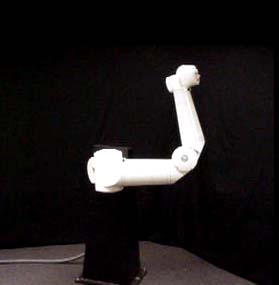
写真:LWRとほぼ同サイズのRobotics Research社製のK-1207iロボット。同社のWebビデオから引用。LWRと比較すると(製造年が10年も前だけに)、加減速度は低いし、騒音も大きいように見える。NASAやFord Motorsで一部実用されたようだ。
1.ねらい
1)手で押して容易に操作できるロボット(教示が感覚的にできる)
2)ロボットのどの部分が人に当たっても大きなダメージを与えないロボット
(ロボットと人の作業領域のオーバラップがある程度可能)
3)ツール端での高速なインピーダンス(またはコンプライアンス)制御特性
4)軽量・大可搬量のロボット(可搬質量≒ロボット質量)
5)7軸で器用なロボット(教示作業が簡単化)
6)関節駆動構造のモジュラー化により低価格化が可能
2.構造
米国Robotics Rsearch社のロボット(K-*i型)との共通点は;
1)7軸
2)関節駆動系の構造
ハーモニックドライブ、モータ、ブレーキ、回転角エンコーダ、関節トルクセンサ(歪みゲージ式)が一体化
3)関節内に関節ごとのサーボコントローラ(DSP使用)とモータドライバを分散配置
4)ハーモニック減速機とモータ回転軸の中空軸心にドライババスと情報通信用のLANケーブルを通す。
5)関節トルク制御方式のインピーダンス制御
LWRの進化したところは;
・アームは炭素繊維強化プラスティックスで軽量化
・モータの小型高出力化
・ハーモニックドライブの出力側にも回転角度エンコーダを配置(減速機の低剛性補償?)
・関節サーボコントローラと運動制御用コントローラとの情報通信用に光LANを採用(注1)
注1:日本で発表されているヒューマノイドロボットは、まだLANを採用していないようだ。産業技術研究所で現在開発中の「ヒューマノイド・ロボットのための実時間分散情報処理」システムでは採用される予定
3.特徴
Robotics Rsearch社のロボットと共通の特徴は;
ツール端に力ートルクセンサを配置したインピーダンス制御に比較してインピーダンス制御の応答速度が向上し、嵌め合いなどの作業速度が数倍に高速化。
アームのどの部分を触ってもアームを動かすことができ(Sensibility along the entire arm structure)、低速での接触ならば人体を傷つけることは少ない。人と作業領域をオーバラップしても安全性が高い(ただし、高速移動状態での人との接触はやはり危険)。
LWRの特に優れた点は、ロボット質量と同じ質量を扱える点。従来の小型ロボットはロボット質量の1/5から1/8程度の質量しか扱えなかった。アームに炭素繊維強化プラスティックスを使った以外にも、減速機に高減速比のハーモニックドライブを使ったことが自重の軽量化に貢献したと思われる。
4.問題点
1)Robotics Rsearch社のK-*i型ロボットは発表されてから既に15年程経過しているのに、いまだに産業用ロボットとして量産に入っている様子が無い。試験用アームとしての位置づけを出ていない。コストパフォーマンスが有利になるアプリケーションが産業用分野では見つかっていないのではないか?数が出ないので、価格が下がらないことが問題だと思われる。LWRはRoborics Rsearch社のK-*i型ロボットより進化していると思われるが、これも発表以来4年程度経っている。関節駆動系にセンサを多用していること、アーム材料に炭素繊維強化プラスティックスを使っていることなどでロボットが高価格になっている。実用的なロボットにするためには再設計が必要であろう。KUKA社の製品として製品化(市販はされていない)されているので、将来には改良されるのではないか?
2)筆者の知識不足かもしれないが、ハーモニックドライブが産業用ロボットのような激しい使用環境で長期のMTBF(故障発生までの平均時間、スポット溶接用ロボットの場合10万時間)が要求される用途に適切な素性を持っているかどうかという点が心配である。今後の耐久性面での改良が鍵を握ると思われる。筆者としては別種の減速機として遊星歯車減速機なども検討する価値があると思う。