12月2~5日に東京ビッグサイトで2015国際ロボット展示会が開催された。最終日(5日、土曜日)にでかけて、産業用ロボットから、サービスロボットの現状を広く見ることができた。
1.関心があったのは、
1)人と協働動作できるロボットco-robot(海外製)
ABB社のYuMi、KUKA社のiiwaシリーズ、Rethink Robotics社のSawyer、Universal Robots社のURシリーズなど
2)人と協働動作できるロボットco-robot(国内製)
デンソーウェーブ(Cobotta)、カワダロボティックス(Nextage)、ファナック(CRシリーズ(4,7kg))、安川電機(HC-10)、川崎重工(DUARO)など
3)ビンピッキング(ファナックをはじめ複数社)、オフラインシミュレータ(ロボットメーカ、他数社)、ORiN(デンソーウェーブ、ORiN協議会)などのソフトウェア
4)災害対応ヒューマノイドロボットの実演
産業技術総合研究所(HRP-2改)、東京大学(Jaxson)、千葉工業大学など(HYDRA)
5)サービスロボット、その他
トヨタ自動車(HSR)、パナソニック(HOSPI)
2.それぞれのロボット詳細について
各ロボットに関しては、過去にもWeb上に動画や写真で説明があったので、このWebサイト(ロボットあれこれ)でも今までいろいろ取り上げてきた。それぞれの動きについては予測はしていたが、今回、実際に触ってみたものについて予測との一致度合などを補足説明する。
1)co-robot(海外製)のダイレクトティーチング特性など
(1)ABB社のYuMi
想像していた通り、ダイレクトティーチングでは、腕は軽くスムースに動かせた。腕を押すのをやめると、ブレーキストップのような感覚で急に止まるのが特徴。ロボットの姿勢から各軸にかかる自重による負荷トルクを計算して、バランスをとっているようだ。アームにはマグネシウム合金が使われており、軽量化に重点が置かれた設計になっている。
(2)KUKA社のiiwa
手で押す操作に非常に滑らかに反応して動く。始動から停止まで、サーボでバランスを制御している(コンプライアンス制御)。押すのをやめると、YuMiのように急に止まるのではなく、スピードが次第に落ちて止まる。アームにはカーボンファイバーが使われており、軽量化を重視した設計になっている。
(3)Rethink Robotics社のSawyer
KUKAのiiwaに近いが、滑らかさでは劣る。ばねが各軸に入っているためか、押すとまずばねが縮んでからサーボが動き出すので、少しぎくしゃくした始動になりやすい。停止はスムースに止まる。
(4)Universal Robot社のUR5型
予想通り、ダイレクトティーチングには海外製の4種のロボットの中では一番力が必要である。これではきめ細かいティーチングをすることは、ほとんど不可能ではないか? 2015年には日本で約100台のUR型が売れたとのこと。販売先は中小企業かと思ったら、日本の場合、大企業が多いとのことで、予想外だった。
2)co-robot(国内製)のダイレクトティーチング特性など
(1)デンソーウェーブ Cobotta
直接アームに触れる機会がなかった。今回初めて一般公開された。アームの大きさから類推するとダイレクトティーチングの操作性はYuMiと同レベルではないか?YuMiは7軸であるがCobottaは6軸の点が異なる。YuMiと似た双腕型も展示されていた。双腕型は腰部に回転と曲げの自由度がある点がYuMiとは異なる。Cobottaの写真とビデオを参照しておく。Cobottaはまだ開発の途中らしく、サーボに細かい振動が乗っていた。
オープンプラットフォームを採用している点が特徴で、誰もがロボットアプリケーションを開発できるとのことである。デモでは音楽に同期してロボットアームがダンスをしていたが、このようなアプリケーションを書ける点が、従来の産業用ロボットにはなかった特徴となっている。ROSのミドルウェアなども使えるようになるのだろう。ユーザから新しいアプリケーションが発明されてくる可能性も十分に期待できる。ロボット機能が新しい展開を始めるかもしれない。面白い試みと思った。川崎重工も同社の7軸ロボット(MS005N)の制御インターフェース(オープンAS)を公開し、MUJINのPick Worksをインストールしてビンピッキングのデモをしていた。同様の試みである。注目してゆきたい。
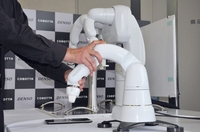
Response.15 (自動車) (11月21日ホームページから引用)
(2)川田工業 Nextage
直接アームに触れる機会がなかった。7軸すべてが80w以下のco-robotである。思ったより小さい印象だった。2014年6月現在で150台以上が売れているとのこと(web週刊ダイヤモンド2014年6月14日号)。
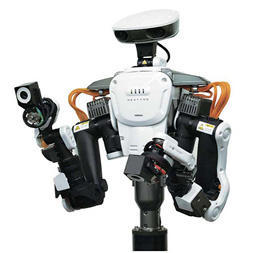
(3)ファナック CRシリーズ
小型協働ロボットとして、今回の見本市で初めて公開された。全軸トルクセンサを装備し、ジョイントトルク制御を行っている。スムースに反応ができる。アームはソフトカバーでおおわれており、衝突時の衝撃を和らげている。可搬加重4kg(CR-4iA),7kg(CR-7iA、CR-7iA/L)の計3種類がある。構造はiiwaのように軽量化されておらず、従来型と同じ設計(リーチ550、911mm、自重20kg,27kg))のようである。
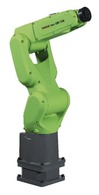
日刊工業新聞 ニュース/ロボット〈2015.12.02から引用)
(4)安川電機 Motoman HC-10
全軸トルクセンサを装備し、ジョイントトルク制御を行っている。スムースに反応ができる。構造はiiwaのように軽量化されておらず、従来型と同じ設計のようだ。
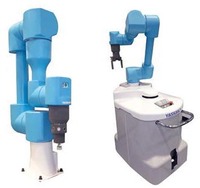
W.マイナビニュース(2015.11.30から引用)
(5)川崎重工 DUARO
直接アームに触れる機会がなかった。スカラ型双腕ロボット。
3.ソフトウェア関連について
1)ビンピッキングビジョンのデモが数多く見られた。
研究の歴史は古いが、ビン状態の部品を識別する技術が相当高まっていることが分かった。ファナックとPFNがファナックのブースで、(株)3次元メディアの3次元ロボットビジョンシステムが安川、川重、三菱、MUJINのブースで、キャノンのマシンビジョンシステムが川重、安川、デンソーウェーブのブースで、それぞれデモを行っていた。
キャノンと3次元メディアのビジョンシステムは「パターン投影による3次元距離画像計測と濃淡画像解析を併用した方法で、部品のCADデータを必要とする。異なるビン状態の対象物を5パターン見せることで準備が完了」する。 キャノンの例では認識時間は2.5秒程(下図、ビジョンシステムの処理)とのことである。
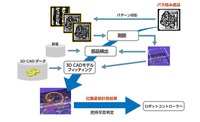
一方、PFN(Preferred Networks社)の方法は、現在注目が高まっているディープラーニング使っている。この方法はCADデータなどを必要としない。「実際にロボットで部品を取らせてみて失敗と成功の画像例をそれぞれニューラルネットワークに学習させてゆく。5000回の学習の後では、ピッキングの成功率は90%程度」になる。認識に要する時間はキャノンの例と同程度と思われる。ただし、この方法の問題点は、学習に要する時間が数時間~数十時間と長い点である。まだ研究途上で実用までにはまだまだ時間を要すると思われる。
2)オフラインティーチングシステム
現在では、ロボットメーカーはティーチング時間を短縮するために、オフラインティーチングシステム(3次元ソリッドモデル)を用意している。しかし多くは、画面上でウェイポイント(waypoint)を指示する必要がある。
一方
、(株)MUJINのティーチングシステム"Pick Worker"はウェイポイントを自動発生し、ロボットの特異点や障害物回避ができる軌跡発生を自動でおこなう。ビン状態の部品箱の位置と部品整列箱の位置を教えるだけで、3次元画像処理システムからの信号を受けて部品をピックし、整列箱の整列することができる。このように、ロボットの知能化が進むにつれて、特定の作業全体をアプリケーションとして販売できるようになる。"Pick Worker"だけでなく、いろいろの作業がアプリとして販売され、ロボットがスマホのように簡単に機能追加できるようになってゆくのだろう。
3)ORiNの利用状況について
ロボット向けのシステム構築支援ソフトウェアであるORiNがどのように利用されているか興味があったので気に留めながら見学した。その結果、表に出してPRしていたのは、メーカーとしてはデンソーウェーブのブースだけであった。その他にORiN協議会が1ブースを使ってPR活動をしていた。これから見ると、ORiNはまだ、他のロボットメーカには広く使われているとは言い難いようだ。広まらないのはロボットメーカが十分にその価値を認識していないからであろう。ORiNが従来方法に対して圧倒的にシステムの準備時間を短縮できることを、いろいろな具体例で示すことができれば、ユーザは競って使うはずである。